There is no shortage of wearable technology with sensors built into them. But what if those wearables and sensors weren’t as noticeable as traditional sensor technology like smartwatches? Scientists are testing eco-friendly sensors inspired by spider silk that go right on the skin.
Web Sensor
Researchers from the University of Cambridge developed a method that directly prints eco-friendly sensors onto biological surfaces. The sensors are also adaptable and subtle. In addition, they are similar to spider webs because they can stink on organic surfaces like human skin or flower petals. According to researchers, the “spider silks” incorporate bioelectronics that allows users to add different sensing abilities to the “web.”
Researchers say the fibers are at least 50 times smaller than human hair. They say the fibers are so light that when they printed them directly onto a fluffy seedhead of a dandelion, the flower didn’t collapse. When they print it onto human skin, the fiber sensors conform to it without blocking sweat pores. A user can wear the sensor without even knowing it’s there. The tests performed on a human finger suggest the sensors can monitor health. Additionally, it is a low-emission and low-waste method of printing for augmenting living structures. There is a range of fields that could use them, including healthcare, virtual reality, electronic textiles, and environmental monitoring.
Human skin is incredibly sensitive; however, augmenting it with electronic sensors could open up a whole new way we interact with the world. For example, the electronic “spider web” sensors could help us understand skin sensations or increase “reality” in video games or virtual reality.
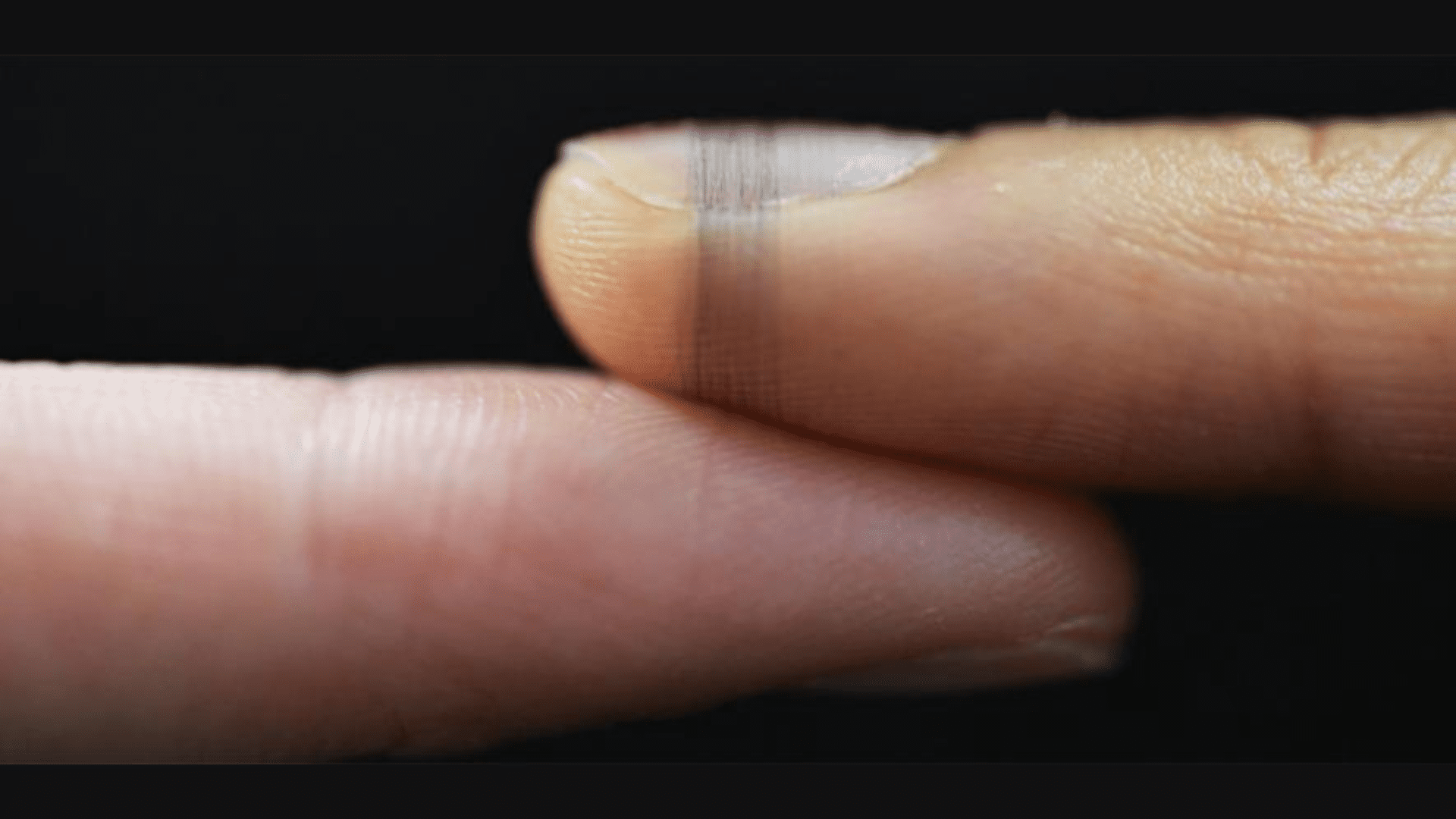
Explore Tomorrow's World from your inbox
Get the latest science, technology, and sustainability content delivered to your inbox.
I understand that by providing my email address, I agree to receive emails from Tomorrow's World Today. I understand that I may opt out of receiving such communications at any time.
Other Methods
Researchers say electronic sensors are more comfortable and less intruding than other wearable technologies, like smartwatches. “If you want to accurately sense anything on a biological surface like skin or a leaf, the interface between the device and the surface is vital,” said Professor Yan Yan Shery Huang from Cambridge’s Department of Engineering, who led the research. “We also want bioelectronics that are completely imperceptible to the user, so they don’t in any way interfere with how the user interacts with the world, and we want them to be sustainable and low waste.”
There are multiple ways to make wearable sensors, but they come with drawbacks. For example, flexible electronics are normally printed on plastic films. Typically, plastic films don’t allow gas or moisture to pass through. According to the University of Cambridge researchers, other researchers have discovered flexible electronics that let gas through, like artificial skin. However, it gets in the way of normal sensations. Additionally, wasteful manufacturing methods rely on a lot of energy.
Of course, 3D printing is another popular route. But, it is not without its faults. While it is less wasteful than other production methods, it creates thicker products. Spinning the fibers produces devices that are not noticeable to the user. However, researchers say the devices don’t have a high degree of sensitivity and are difficult to transfer onto objects.
Spider Silk Method
The Cambridge researchers found a new way to make high-performance bioelectronics for biological surfaces. They print the material directly on surfaces like human skin or flower petals. The researchers take inspiration from spiders, which use minimal materials but create strong and sophisticated structures for their surroundings.
Using a biocompatible conducting polymer, hyaluronic acid, and polyethylene oxide, the researchers spin their bioelectronic “spider silk.” Researchers can control the spinnability because the fibers are produced from a water-based solution at room temperature. The orbital spinning method allows the fibers to morph into living structures, down to human fingerprints.
“Our spinning approach allows the bioelectronic fibers to follow the anatomy of different shapes, at both the micro and macro scale, without the need for any image recognition,” said Andy Wang, the first author of the paper. “It opens up a whole different angle regarding how sustainable electronics and sensors can be made. It’s a much easier way to produce large area sensors.”
According to the Cambridge team, the sensors simply wash away at the end of life. In addition, they can repair the sensors at any time and in any place.
Huang said, “These sensors can be made on-demand, right where they’re needed, and produce minimal waste and emissions.”