Gyroscopes are the epitome of “deceptively simple.” At first glance, it looks like a complex top, with the main gimmick being that if the wheel is spinning, the orientation of the axis won’t change. But it’s more than just an executive desk toy–it’s a vital component for many of our most powerful and fragile devices.
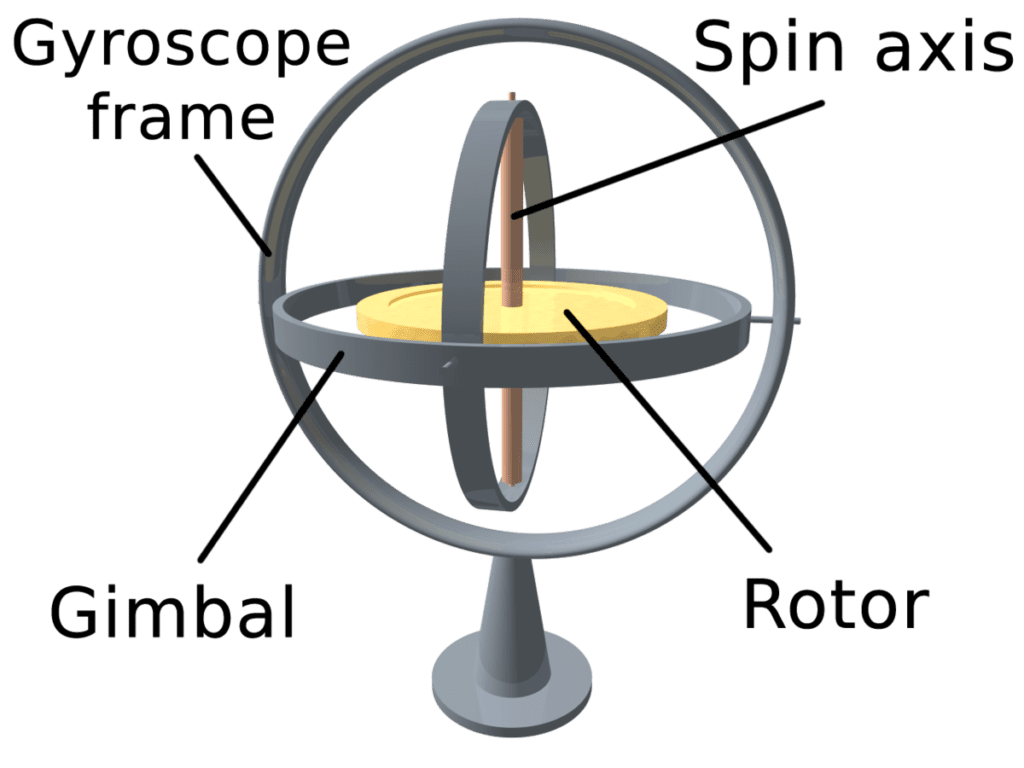
Because of the wide variety of gyroscopes, there’s no one raw material that can be listed. Some are cheaply made while others use precious gemstones. The central wheel may spin on ball bearings or compressed air. There are even some that exist in a vacuum, suspended by an electrical current to prevent friction from building up. It all depends on what the gyroscope is used for.
However, all gyroscopes have the same basic components, particularly if they’re powered by electricity. There’s the motor, the electrical components, electronic circuit cards for programming, and the axel and gimbal rings. Some of these, like the motor, are supplied by subcontractors or may be stock items. The gimbals and axels are custom-built by the manufacturer. Aluminum is widely used due to its strength and expansion, but titanium is common for more advanced gyroscopes.
The metal choice may also be influenced by design. The design mainly focuses on what wheel should be used for the gimbal, often drawn from a preexisting selection of designs. It’s rare for a manufacturer to build a new design from scratch; most prefer to adopt an existing design for their product. However, each design must be carefully studied and thorough. There’s little room for error, as the gyroscope must have a uniform cross-section in order to remain balanced.
Once the design is finalized, it’s time for production. The gimbals and gimbal frames are cut out from the metal of choice and polished before being stored for assembly. Next comes the motor, as gyroscopes are typically built from the inside out. The average gyroscope motor needs to spin at 24,000 RPM (revolution per minute). It’s tested multiple times to ensure that minimum can be met. Gimbals and frames are assembled and attached next, still working outwards. Bearings are put into place, and the outermost electrical connections and circuit cards are added. Finally, the gyroscope is calibrated and checked by hand.
Quality control is arguably the most important part of manufacturing a gyroscope. Gyroscopes are in everything from cars to weapons and could cause terrible destruction should they fail. For this reason, assembly line workers must be tested and given training before being hired, with additional training during their tenure. Quality standards are measured throughout the production process, with outside inspectors being brought in for the most important checks. The vitality of quality assurance is so high with gyroscopes that government inspectors are known to review them. In many cases, customers perform their own tests, returning the gyroscopes that aren’t up to snuff.
It’s worth mentioning that, unlike the production of many components, creating a gyroscope doesn’t produce much waste. Some chips may be left over from the machining of the gimbals and bearings, but these are returned to the metal supplier for recycling. Manufacturing them is also fairly safe, despite the training the employees must go through. The most that needs to be done is humidity control to prevent static buildup.
Gyroscopes are easy to understand but difficult to manufacture. Without them, however, many machines and vehicles we take for granted would never be able to function. It’s everything from keeping a plane from crashing to making a Steadicam, well, steady. It’s the laws of physics, and even as technology evolves, it will remain ever balanced.
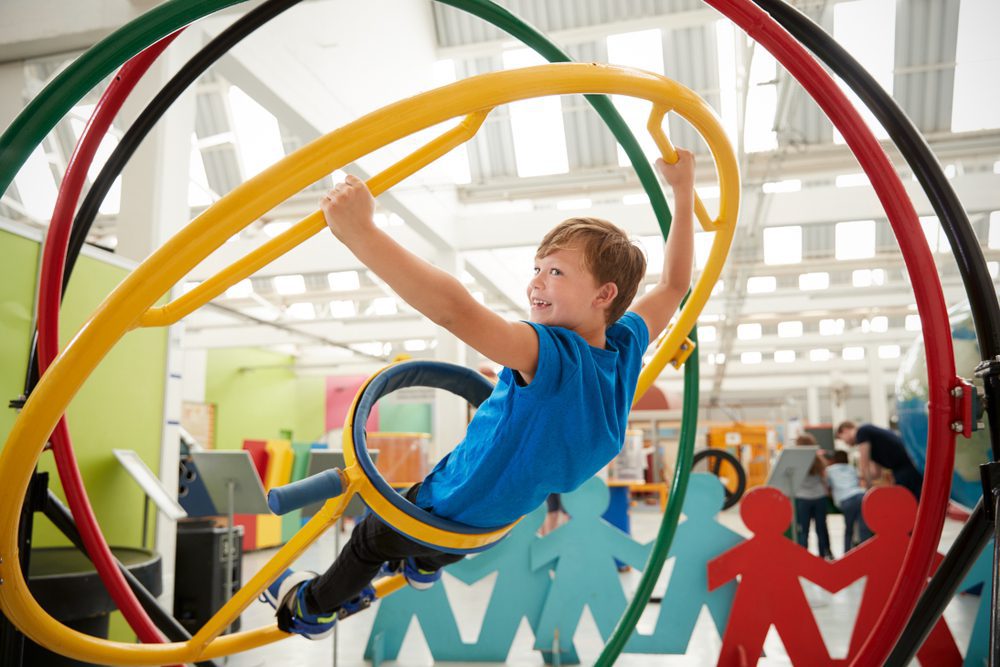
Learn more about the World of Production, and discover how microchips, anamorphic art, and game controllers are made.