What can be learned from Helmerich & Payne’s (H&P) 103 years of experience as a drilling contractor? H&P’s VP of Engineering, Joel Ferland, and Director, Global Engineering Support, Chris Major, talked to Tomorrow’s World Today about the story of one of the most pivotal moments in land drilling innovation and what the future holds for the global FlexRig® fleet.
Tomorrow’s World Today (TWT): How did the FlexRig® fleet come about?
Chris Major (CM): The locomotive industry was using new technology on their alternating current (AC) drives. It was revolutionary for them, and as we decided to develop an application for our industry in the late 1990s and early 2000s, the AC drilling rig was born. Creating a drilling rig with a top drive integrated to an AC drive system, deployed in a scalable fashion – it became revolutionary for us as well.
It was not a popular move at first, but we wouldn’t be able to drill today’s modern wells without top drives. It was a bold decision that had a global impact – a monumental commitment in many ways, full of challenges, but as a company we were committed to doing the right thing.
Pad drilling was a solution to address a customer’s need: multi-well rows. On land at the time, single wells would be drilled in a row. But even then, it wasn’t prevalent. When the FlexRig fleet was developed, it led the industry as the first purpose-built rig for pad drilling.
Joel Ferland (JF): We were the first of our kind to design rigs for our specific needs and the needs of our operators. We were also the first to use in-house engineering design. Our manufacturing capabilities allowed us to become a large-scale manufacturer capable of producing hundreds of drilling rigs in a short amount of time.
TWT: What has contributed to the longevity of H&P and its success in the drilling industry?
JF: The one thing that has enabled us to be so nimble and change with the market has been the standardization of our fleet. A crew on one rig can go to the next, and it’s identical. They know where everything is located and how to operate it, and it allows us to rapidly implement new processes and technology at scale. A single solution is deployed on all our rigs: we don’t have to do it iteratively.
TWT: How are you taking the H&P legacy of the past 100 years and applying it to the next 100 years?
CM: The future is determined by data-driven decisions. We consider the wells currently being drilled, but our primary focus is on the next generation of wells.
JF: We always ask ourselves, “How can we do things better? How can we keep our people safer?” Those themes, guided by our innovative spirit, will carry us through the future. This evolution of robotics initiatives and increased automation creates a chain reaction of new opportunities for improvement, like challenging us to implement better maintenance processes so our equipment continues to run properly.
CM: We’re regularly drilling two and a half mile laterals and now drilling three, even four-mile laterals. Manually tripping 8,000 meters of pipe has a cumulative impact on the body. We’ve always said, “We want people to use their brains and not their brawn.” We’re innovating to make each task less physically intensive.
JF: Automation allows us to drill wells repeatedly and consistently across an entire fleet of rigs. We all win in the end.
We’re always looking at different technologies – staying mindful of what’s going on and what’s different. We investigate innovative technologies, some not even directly related to the oil and gas industry but could be adapted to our framework.
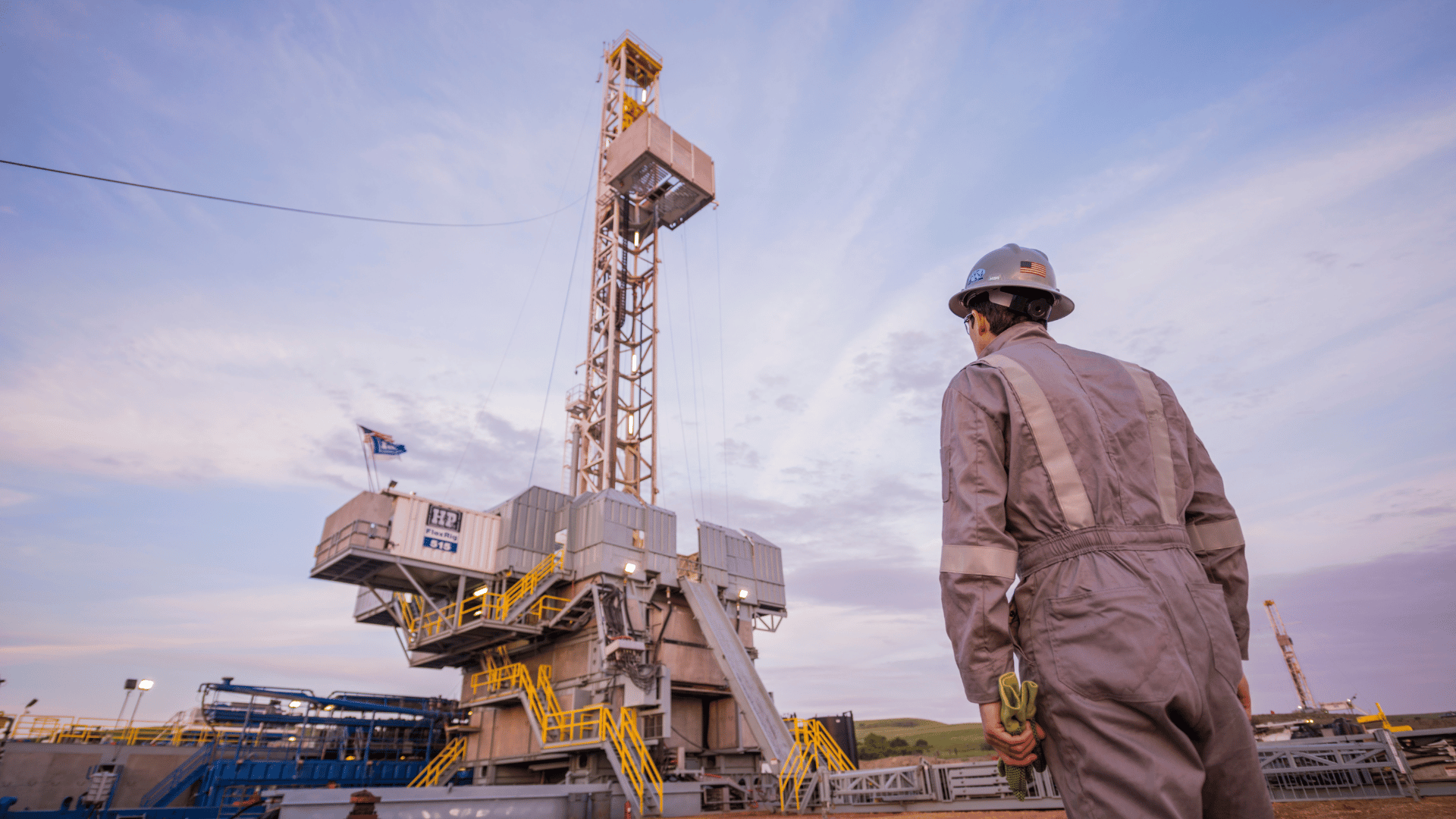
TWT: How did you take learnings from the design process of the early FlexRig® fleet as you developed the newest addition: your walking rigs?
JF: Safety by design. When we designed our walking rig, we considered the frequent task of driving pins on a substructure during rig moves. ISO lock systems, native to the container industry, remove the need for a sledgehammer. We reduce exposure to serious injuries and fatalities through continuous improvement like this.
It was a team effort from the beginning: engineering, manufacturing, operations, and, most importantly, the field. The end user of your product has the best input. We take pride in our ability to be our own internal customer.
CM: As we implement new initiatives, we reflect upon our historical journey as a company. It’s an honor to bring others alongside us on this path towards the future of the energy industry.
For more information on innovations in the drilling industry, check out the full episode below: