As the world rapidly embraces gains in technological innovation and sustainability, the oil and gas industry is no exception. Automation—using technology to replace human interaction—is a game-changer, leading to significant step changes. Taking a closer look at how automation is revolutionizing the oil and gas drilling process reveals a safer, more efficient, and more environmentally responsible energy industry than ever before.
The oil and gas industry’s automation evolution
Automation within the oil and gas industry is evolving rapidly. Historically, drilling operations involved intense physical and mental labor with rigorous supervision. Advancements in technology, computing power, and data analytics have drastically changed which provides for safer and more enjoyable career opportunities in drilling operations.
Autopilot…on a drilling rig?
The oil and gas industry has multiple paths for incorporating automation. One noticeable example is the transition from the edriller system to an autodriller system. Think of the autopilot function used on an airplane—the autopilot incorporates advanced electronic and digital technologies into flight operations, while still requiring a pilot in the cockpit. An edriller system does the same for drilling wells, with a driller standing by in a “cockpit” called the Driller’s Cabin. Taking the edriller a step further in innovation, an autodriller system is responsible for also automating certain aspects of the drilling process, requiring even less human intervention.
H&P’s model-based autodriller, Autodriller Pro, promptly responds to many problems that occur while drilling, commonly called “disruptions,” with a focus on an increased rate of penetration (drilling faster). This also prolongs the life of the drill bit, which is much larger and more expensive than what you would buy at a hardware store! Making the process of drilling a well more predictable and consistent allows for better planning of operations, called “well programs,” which can take years to complete. A 20 percent increase in the rate of penetration (drilling the well 20 percent faster) can have a significant impact on a budget and schedule.
Rig floor automation
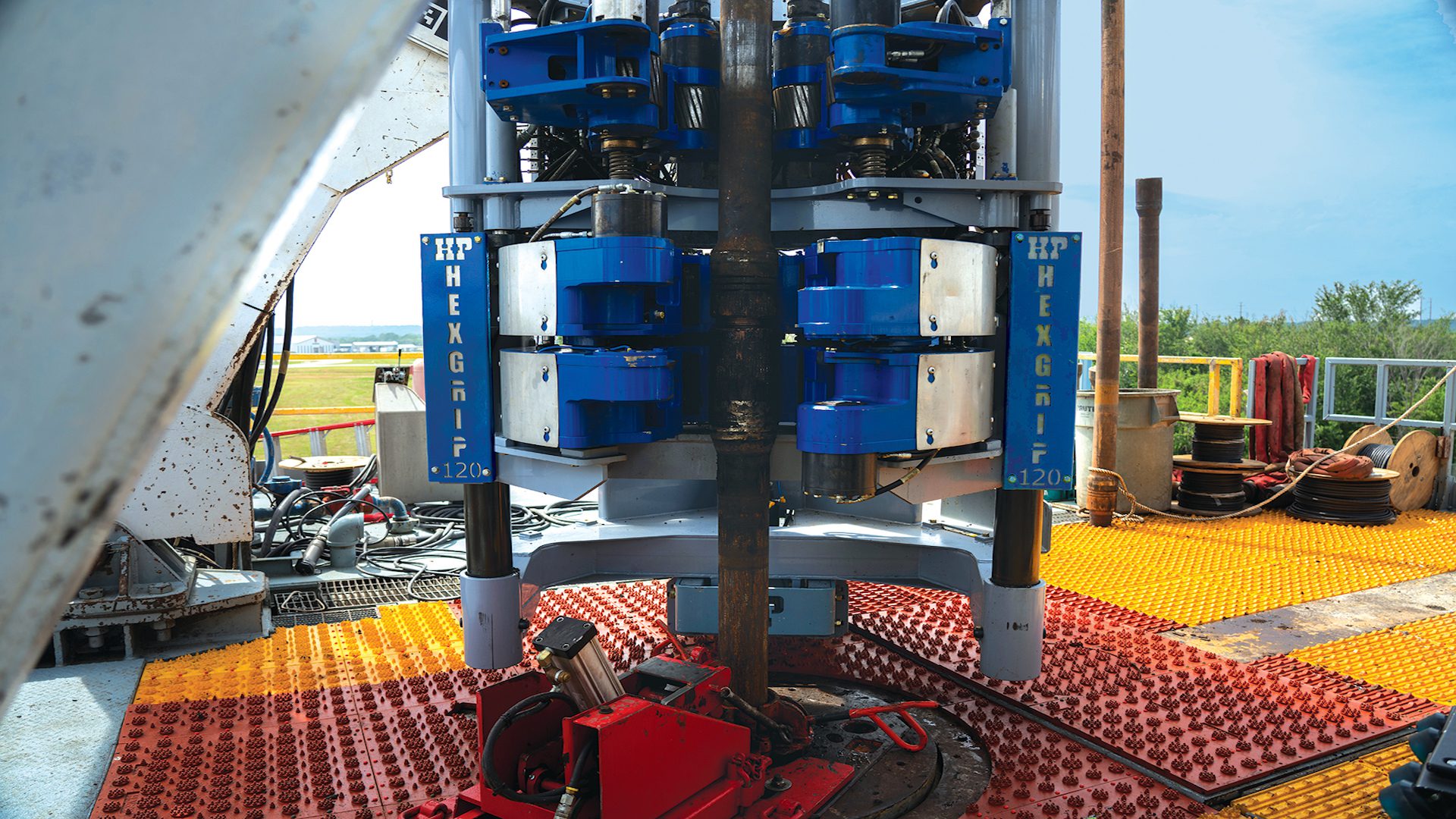
Another exciting example of innovation is the automation of the rig floor. The rig floor is an area on a drilling rig where the fast-paced task of connecting long sections of drill pipe occurs as the well is drilled deep below the earth’s surface. Equipment on the rig floor has enough power to maneuver long strings of drillpipe weighing thousands of pounds from the ground up to the rig floor, making it the center of well operations and activity. Automating equipment on the rig floor creates consistency through process automation and removes physical labor. Consistency leads to optimization opportunities as well as safety and environmental benefits.
Fitted with sensors and data collection capabilities, the system adapts processes to sustain ideal results when changes occur, such as a change in drillpipe connection. H&P’s Rig Floor Automation generates ample data, identifying patterns and trends tied to processes. Just as with other industries, data collection through digital transformation contributes to informed decision making. Digital transformation and automation are closely related concepts that often complement each other to drive efficiency, innovation, and competitiveness in various industries. This synergy leads to more innovative, efficient, agile, and data-driven processes that drive business success in today’s rapidly evolving digital landscape.
Automation’s impact on safety and sustainability
One of the most significant advantages of automation in drilling processes is its positive impact on safety and environmental responsibility. Remote drilling control minimizes the need for human presence in potentially hazardous areas on drilling sites. Optimization of the control system correlates to a reduction in risk of accidents and exposure to hazardous conditions.
As automation optimizes drilling operations, the amount of energy required to produce oil and gas is reduced, as well as carbon emissions. Further gains can be seen when engine management systems reduce excess engine use, which also reduces greenhouse gas emissions for the power required to drill a well. H&P’s entire FlexRig® fleet of rigs is capable of utilizing utility grid (also known as high line) power, providing a more efficient option for powering the drilling rig.
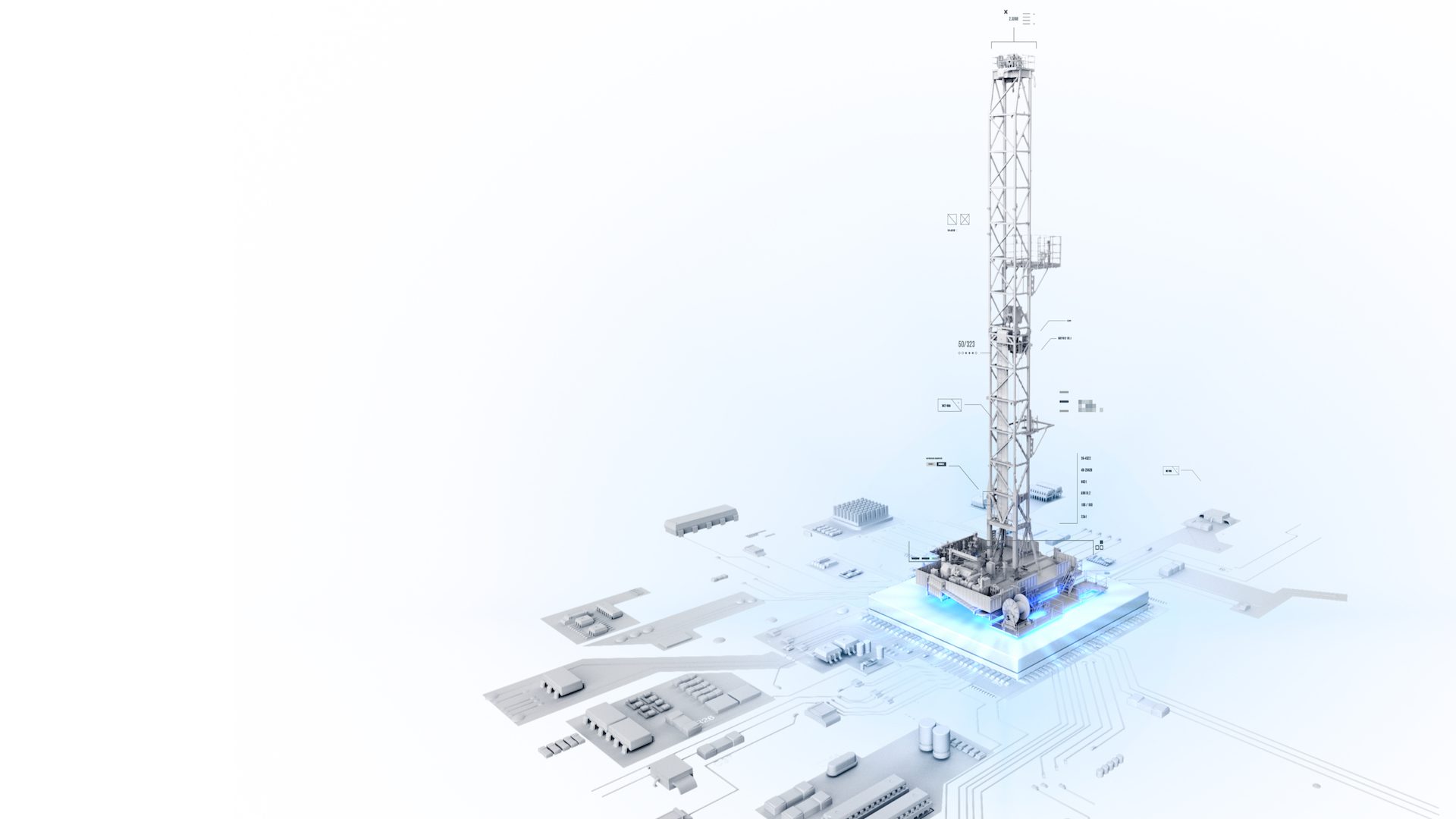
Looking towards the future
While automation in the oil and gas drilling process has great potential, challenges remain. These include cybersecurity risks, the need for a skilled workforce to manage automation systems, and a generally skeptical approach to change across the industry. However, industry leaders are committed to addressing these challenges in different ways.
Automation is actively redefining the oil and gas drilling process. Reducing the need for human intervention makes drilling wells safer, more environmentally friendly, and economically viable—all while transforming the roles and tasks of humans on the drilling rig, uncovering new areas for technological innovation. An improved work environment combined with the removal of a physical presence on the rig floor creates opportunities to redefine roles in drilling operations for future generations. As the industry continues to embrace automation technologies, we can expect even greater advances, transforming tomorrow’s world of energy production for the better.
For more information on the innovations in the drilling industry, check out our full episode.