Concrete has been a cornerstone of infrastructure for centuries. It’s the foundation of many things, from ancient pyramids to modern skyscrapers. However, its use significantly contributes to global emissions. Researchers say it accounts for 9% of the total greenhouse gas emissions globally.
A team of designers, materials scientists, and engineers from the University of Pennsylvania wants to change that with a new concrete that addresses environmental challenges.
3D-Printed, Sustainable, Carbon Sucking Concrete
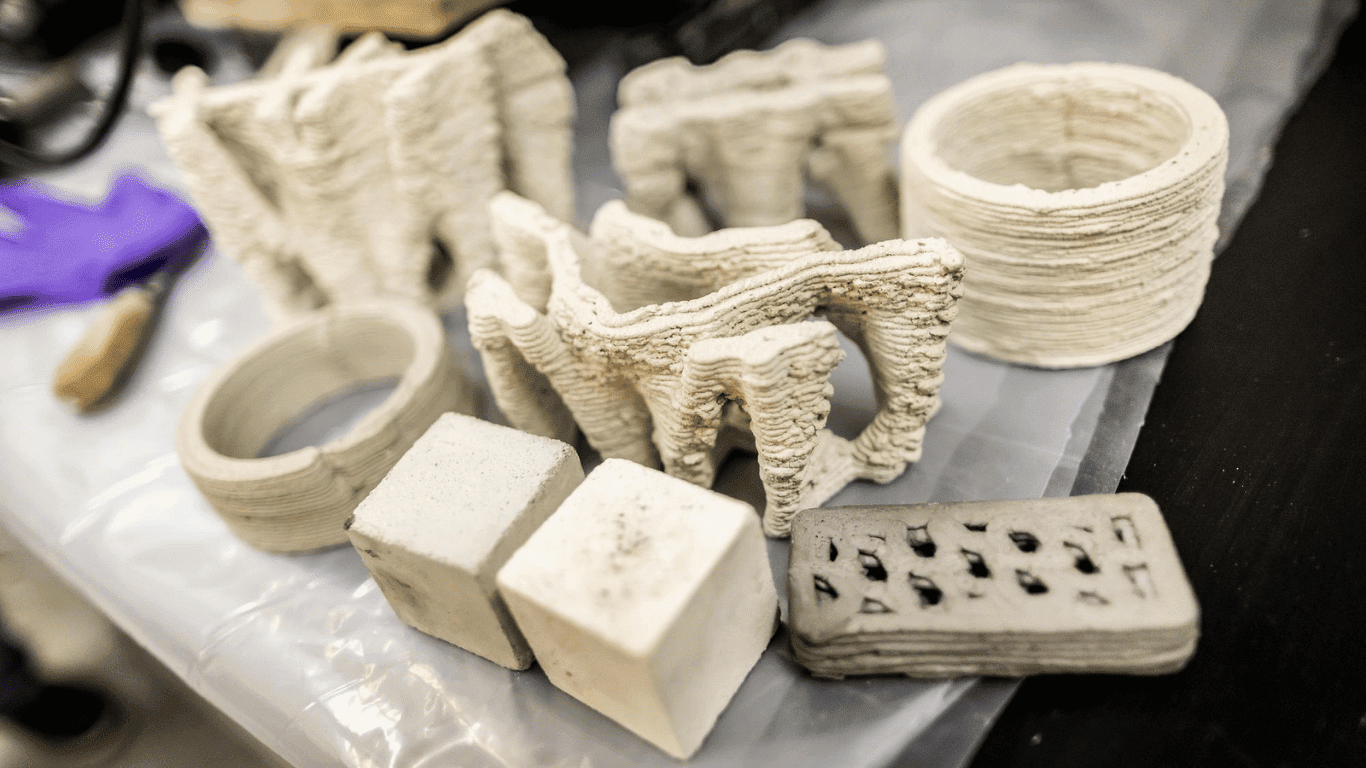
Researchers reportedly combined 3D printing with the fossil architecture of microscopic algae to create the innovative concrete. According to the press release, the concrete is lightweight yet structurally sound. Additionally, they say it captures up to 142% more carbon than conventional mixes, but uses less cement. Despite the lack of cement, it still meets standard strength targets.
The key ingredient is diatomaceous earth (DE), which is made from fossilized microorganisms. DE is a popular filler, and researchers found that it improves the stability of concrete during 3D printing. Its porous, sponge-like texture has pockets to trap CO2.
The team published their findings in Advanced Functional Materials. They believe the concrete could pave the way for a more sustainable yet sturdy building material. In addition to building skyscrapers and bridges, it could help restore marine ecosystems and capture carbon.
“Usually, if you increase the surface area or porosity, you lose strength,” said Professor and co-senior author Shu Yang. “But here, it was the opposite; the structure became stronger over time.” Additionally, she notes that the team achieved a 30% higher CO2 conversion while maintaining the strength of traditional concrete.
“It was about unlocking a new structural logic,” said co-senior author and associate professor of architecture, Masoud Akbarzadeh. “We could reduce material by almost 60%, and still carry the load, showing it’s possible to do so much more with so much less.”
The team also integrated triply periodic minimal surfaces (TPMS), mathematically complex structures found in natural elements like bones and coral reefs. They used TPMS to maximize the surface area and structure while limiting the amount of materials they used. As a result, they used 68% less material than traditional concrete blocks. Amazingly, they increased the surface-area-to-volume ratio by over 500%.
The final product achieved 32% higher CO2 uptake per unit of cement.
Looking ahead, researchers want to scale up to full-scale structures to explore applications in marine infrastructure, such as artificial reefs.
Yang said, “The moment we stopped thinking about concrete as static and started seeing it as dynamic, as something that reacts to its environment, we opened up a whole new world of possibilities.”