Researchers at the University of Texas at Austin developed a groundbreaking 3D printing method that integrates soft and hard materials into a single object. Their method mimics natural structures like bones or cartilage. This new technique uses a custom liquid resin and dual-light system. Violet light turns the resin into a stretchable material similar to rubber, while higher-energy ultraviolet light simultaneously makes it rigid.
Their system allows objects with distinct soft and hard zones to be created in a single print. This method overcomes a common problem: material failure at interfaces. In addition, the method is reportedly faster, more precise, and uses a simple and affordable printing setup. Researchers say there are significant implications for future prosthetics, flexible medical devices, and stretchable electronics.
The Flexible Future of 3D Printing
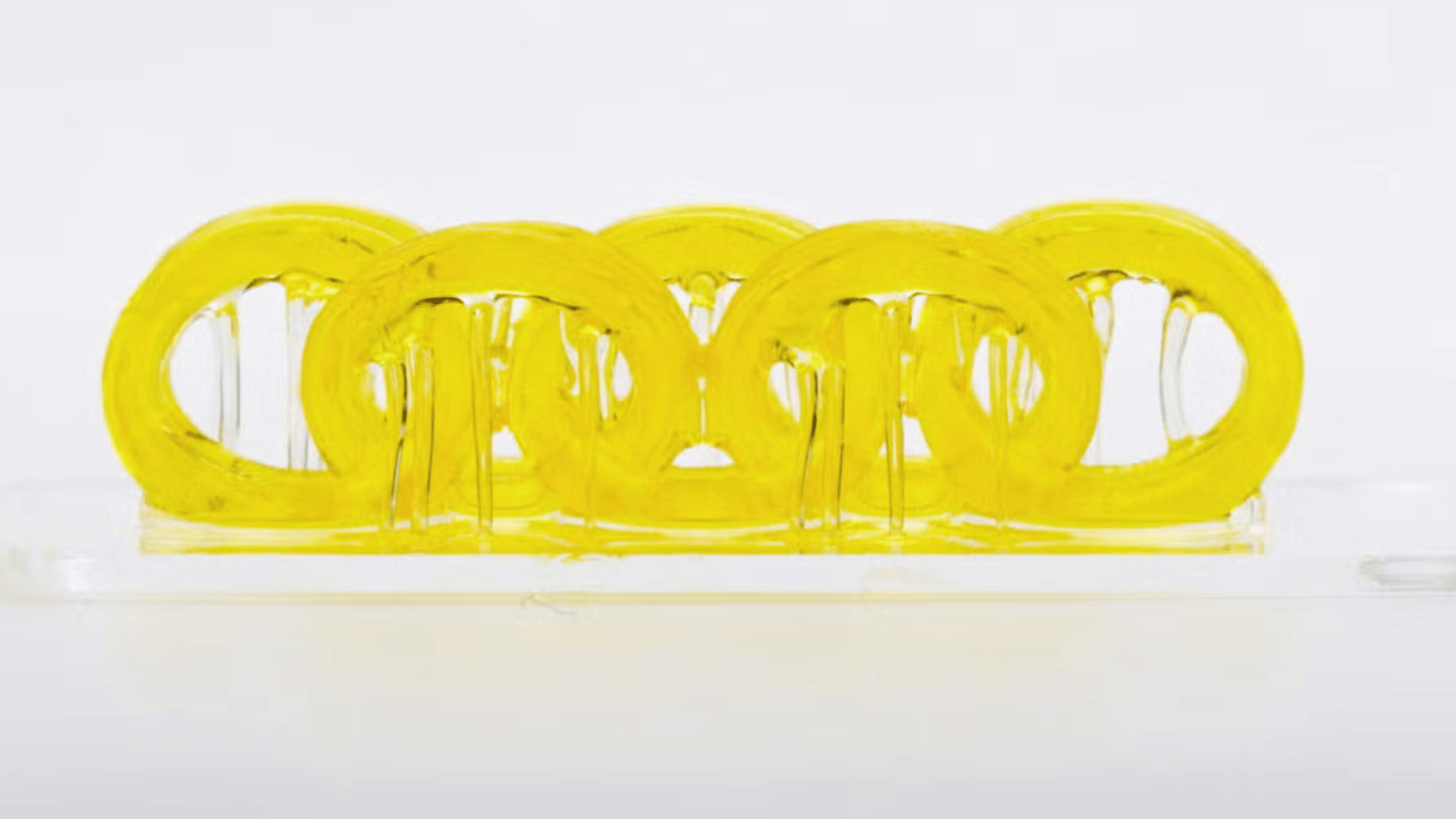
Future prosthetic limbs could move with the natural fluidity of a human joint, or medical devices could become so adaptable that they seamlessly integrate with the body’s tissue. This was once a distant dream, but the researchers took a step closer to it becoming a reality.
The research team was inspired by the blend of toughness and flexibility found in natural structures. They dedicated their work to replicating structures, such as how bones and cartilage integrate.
“What really motivated me and my research group is looking at materials in nature,” explains Zak Page, an assistant professor of chemistry at UT Austin and corresponding author. “Nature does this in an organic way, combining hard and soft materials without failure at the interface. We wanted to replicate that.”
Having the capability of creating objects with distinct zones of varying hardness and flexibility, all within a single printing process, solves a major hurdle in multi-material 3D printing. Traditionally, materials fail where they meet.
“We built in a molecule with both reactive groups so our two solidification reactions could ‘talk to each other’ at the interface,” said Page. “That gives us a much stronger connection between the soft and hard parts, and there can be a gradual transition if we want.”
The UT Austin team demonstrated one of the many potential applications. They created a functional knee with flexible ligaments and rigid bones that move together. The team even developed a prototype stretchable electronic device. Researchers described the breakthrough in a paper in Nature Materials.
“This approach could make additive manufacturing more competitive for higher-volume production compared with traditional processes like injection molding,” Keldy Mason, a graduate student in Page’s lab, explained. “Just as important, it opens up new design possibilities.”