Rolls-Royce is piloting a unique recycling effort by turning old aircraft parts from the United Kingdom Royal Air Force (RAF) into metal powder for additive manufacturing.
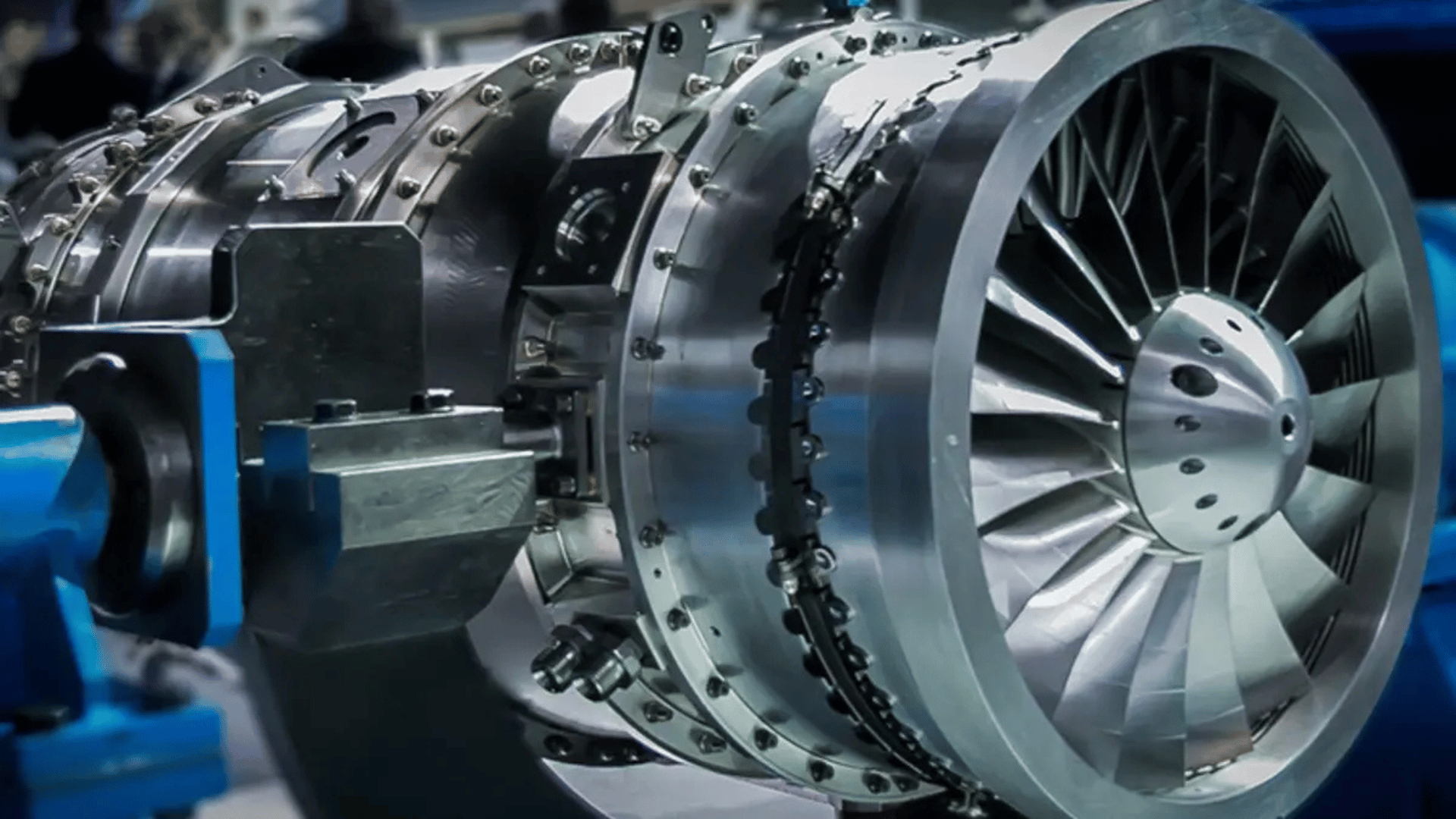
The Tornado 2 Tempest project aims to repurpose retired RAF Tornado components into powdered metal, which are then used to 3D print parts for Rolls-Royce’s Orpheus small engine concept. According to the firm, since Orpheus is part of the Future Combat Air System (FCAS) program, the project showcases the viability of a sustainable approach to defense engineering.
“Tornado 2 Tempest is a bold, exciting, and innovative project and a demonstration of how excellent collaboration between the MOD, industry, and SME can deliver sustainable and technologically advanced solutions,” said Andrew Eady, Rolls-Royce VP FCAS Sustainability, in a statement.
Surplus Ministry of Defence (MOD) assets, such as spare or broken components, often contain valuable metals such as aluminum, titanium, and high-quality steel. The researchers behind the project wanted to explore whether these materials could be atomized into powders, also known as “feedstock,” and repurposed for 3D printing.
To test this idea, surplus components, such as jet engine compressor blades with high titanium content, were cleaned, converted into powder, and used to construct a 3D-printed nose cone and compressor blades. Rolls-Royce installed the nose cone onto an Orpheus test engine and successfully ran it under test conditions to confirm its safety and performance.
The team also featured a Digital Product Passport, which monitors material provenance and lifecycle data. This is designed to enhance the efficiency and effectiveness of material allocation decisions and prevent the use of counterfeit materials.
The project offers potential benefits to the defense industry as it could increase access to critical metals and mitigate the reliance on mining new raw materials.
“Not only can this solution reduce the costs and burden of sourcing critical and high-value metals, but it can also produce components that are lighter, stronger, and longer lasting than those made through traditional forging techniques, thereby further enhancing the MOD’s overall sustainability and effectiveness,” said Thomas Powell, DRDT’s Strategic & Submarine Recycling Senior Commercial Manager, in a statement.