Advanced 3D printing technologies from the United Kingdom Atomic Energy Authority (UKAEA) could help develop essential components for nuclear fusion power plants. UK officials say the Atomic Energy Authority has commissioned two 3D printing machines at its Central Support Facility (CSF).
Accelerating Nuclear Fusion Technology
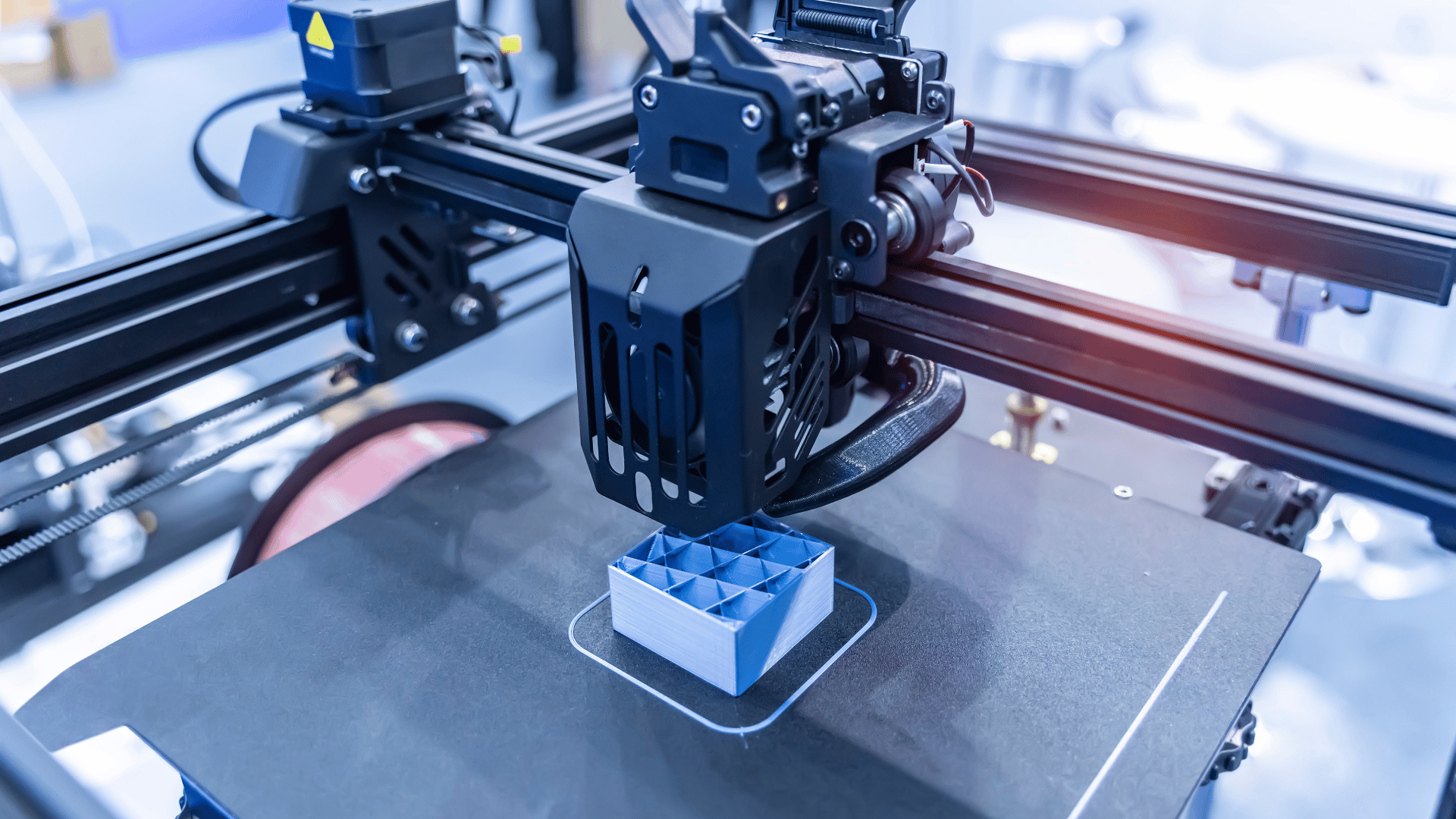
Fusion energy has significant promise for future low-carbon energy. However, the technology must withstand extreme conditions, such as high temperatures, intense neutron loads, and powerful magnetic fields. Researchers explain that traditional methods struggle to produce the necessary material combinations and precise engineering for the specialized parts.
3D printing is intended to change that and address the challenges of the critical complex materials.
Officials believe additive manufacturing, better known as 3D printing, is well-suited for producing intricate materials in low volumes. They say it is ideal for the fusion industry because each machine is custom-made with unique parts. The UKAEA believes 3D printing can cut the costs of precision manufacturing.
3D Printing Technology
One of the new machines is the eMELT Electron Beam Powder Bed Fusion (E-PBF) additive machine. The machine is from Freemelt, a producer of advanced 3D printers. It utilizes electron beam technology to turn powdered tungsten into solid components. Officials say they will use the E-PBF to layer tungsten onto other materials such as copper chrome zirconium, stainless steel, and Eurofer 97. According to researchers, Eurofer 97 is a specialized steel designed for fusion applications.
The second machine is the Nikon SLM280 Selective Laser Manufacturing (SLM) machine. It is used for the experimental production of complex components for successful fusion plants.
According to officials, both 3D printing machines will support the production of plasma-facing components, which are exposed to extreme temperatures during operation. The machines will reportedly decrease the reliance on traditional techniques like welding. Their goal aims to reduce the number of manufacturing and joining processes.
“Future fusion power plants will require thousands – or even millions – of components with complex geometries that can withstand the extreme conditions of a fusion environment,” said Roy Marshall, the head of Operations for Fabrication, Installation, and Maintenance at UKAEA. “UKAEA believes that additive manufacturing will be essential to developing these components at a scale that makes fusion commercially viable.”
He also notes the unique advantage of having electron beam and selective laser manufacturing under the same roof. Marshall calls it “a first for the fusion industry.”