Remote desktop tools allow manufacturing companies to resolve technical issues without physical presence. Production facilities use these applications to access computers from different locations, fix problems quickly, and minimize equipment downtime. As manufacturing processes become more digital, reliable support software becomes vital for maintaining operations. While TeamViewer has been a standard option, many manufacturing firms search for alternatives due to cost concerns or specific feature requirements.
Key Features of Remote Desktop Support Software
Remote desktop support tools must include several core capabilities to serve manufacturing needs. Screen sharing allows IT staff to see what machine operators see, making issue diagnosis faster. File transfer functions let support teams move technical documents between systems without email attachments. Remote control gives technicians direct access to fix issues, while chat features maintain communication during critical troubleshooting sessions.
Security stands as the most vital component. Reliable solutions use encryption to protect sensitive manufacturing data during transfers. They implement access controls to prevent unauthorized entry. Session recording capabilities create audit trails for compliance purposes. Multi-factor authentication adds another security layer for production environments where intellectual property must be protected.
Performance factors matter, too. Tools with low latency provide smooth interactions regardless of factory location. Those with minimal bandwidth requirements work even with limited connectivity on shop floors. Cross-platform compatibility ensures support across Windows, Mac, and industrial control systems, which manufacturing companies increasingly need for their production technology ecosystem.
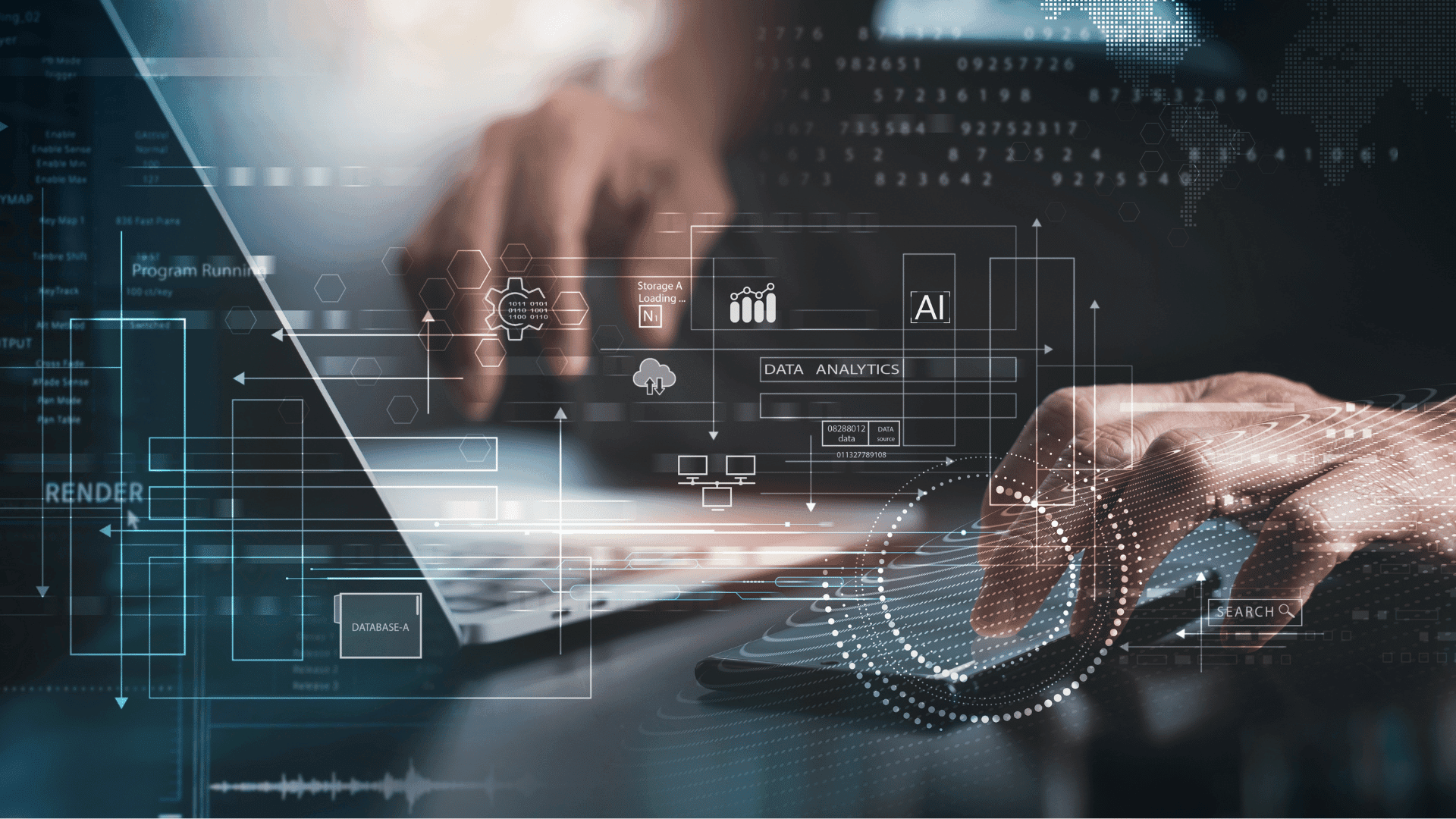
Cost Considerations for Remote Support Tools
Price structures vary widely among remote desktop applications. Some vendors charge per technician, creating predictable costs that scale with support team size. Others use connection-based pricing, which works well for manufacturing organizations with few simultaneous support sessions. Enterprise packages often come with flat-rate options for unlimited connections across multiple production sites.
Hidden costs exist beyond the base subscription. Add-on features like advanced security might carry extra charges. Storage for recorded sessions sometimes incurs additional fees. Consider the total expense, including these potential extras, when comparing solutions.
Free options exist with basic capabilities, but these typically limit session duration or concurrent connections. For small manufacturers with occasional support needs, these limitations might be acceptable. Larger production facilities should examine the top alternatives to TeamViewer for solutions that balance cost with necessary features. TSplus offers one such option, providing remote support tools at competitive rates without sacrificing the security or performance required in manufacturing environments.
Integration with Existing Manufacturing Systems
Remote support tools work best when they connect with other manufacturing applications. ERP integration allows technicians to access machine data directly from business systems. This creates a streamlined workflow from problem report to resolution without disrupting production. Authentication system connections let manufacturing firms use existing user accounts rather than creating separate credentials.
Equipment management compatibility helps track which machines receive support and maintains accurate records of maintenance history. MES integration links production information with support sessions, giving technicians context about manufacturing processes. Session data can flow back to these systems, creating complete records of technical interventions.
API availability matters for custom integration needs. Robust APIs let developers connect remote support functions with proprietary manufacturing systems.
Security Protocols for Shop Floor Access
Security forms the foundation of trustworthy remote desktop support in manufacturing. Connection encryption prevents data interception during sessions. The strongest solutions use TLS 1.3 or similar protocols to secure all transmitted information. User permission requirements ensure technicians only access production systems with explicit approval from floor managers.
Session limitations provide additional protection. These include automatic timeouts for inactive connections and restrictions on what actions technicians can perform on critical equipment. Comprehensive audit logs record who accessed which machines, when, and what actions they took during support sessions.
Compliance features help manufacturing organizations meet regulatory requirements. ISO-compliant tools include data protection measures and appropriate security controls. Industry-specific solutions offer extra safeguards for regulated manufacturing environments. Each sector has specific regulations, so production companies should select tools that address their particular compliance needs.
Implementation Strategy for Manufacturing Environments
Manufacturing companies require specific approaches when deploying remote support tools. A phased rollout works best, starting with non-critical systems before extending to production equipment. This method allows IT teams to address issues without risking essential operations. Creating clear usage protocols helps prevent unauthorized access to sensitive manufacturing assets. These protocols should specify which staff members can authorize remote connections to critical machinery.
Technical considerations include network segmentation to separate production systems from general IT infrastructure. Bandwidth allocation ensures remote support activities do not interfere with production data needs. Training programs must address both IT staff and machine operators, teaching proper authorization procedures and basic troubleshooting steps.
Change management becomes crucial when implementing new support tools. Production supervisors need to understand how remote access helps rather than hinders their work. Documentation of successful interventions builds trust in the system.
This is a sponsored post by Web Key Digital. All reviews and opinions expressed in this post are not based on the views and opinions of Tomorrow’s World Today.